Upgrade Power Supply with Fan Cooling.
After a bunch of years - in the middle of a long running 3D print, my printer suddenly stopped. The bed fell to the ground, well the base of the printer, with a bang.
My first thought was - Oh crap. Now I need a new 3D printer and can't really afford it at the moment. After the initial panic went away, my second thought was - Maybe it is only the power supply, a little optimism newer hurts. So I measured the output voltage of the power supply and got nada.
So I went shopping for a replacement. The specifications of the old power supply was: 12V / 5.3A.
Although I normally go to Conrad.nl for that kind of shopping, I was not able to find any good replacement. The search functionality at Conrad.nl really sucks. So I went to Bol.com and found a 12V / 6A replacement. Well a little more power couldn't hurt, so I ordered the power supply.
The new power supply was delivered next very day and of course had to be tested, so I found a simple object to print.
To my big disappointment my 3D printer stopped again after about an hour of printing. Damn - Maybe it was not only the power supply that had failed after all. When picking up the power supply to check the connections, it was hot as Hell, so it had obviously over heated and shut down.
It's of course good the the power supply have thermal shut down, but it should be able to run continuously at its max ratings.
I tried to let the power supply cool down and did another test print. This time it finished without issues, but the power supply was again way too hot.
So though the specifications for the power supply was on the good side and the Bol.com site stated that the supply should be usable for 3D printers, the closed enclosure, without any air vents, caused it to over heat. Not very handy for a 3D printer supply that is supposed to be able to run continuously for several hours or sometimes even days .
Because the power supply "only" gave up on long running prints, I decided to try to add some active cooling to the supply.
Getting the case open was a little bit of an issue. I thought it was one of these thermo clued cases thar are impossible to open - so I went for my hack saw and gingerly started to hack the case open. Got in - and realised that the case was clipped together not glues. Well too late and I was in.
There were 3 very small cooling fins. One glued to the top of the output transformer. One on the input MOS-FET and the last one, the smallest, on the output rectifier diode.
It was the cooling fin on the output rectifier diode that got very hot.
Fortunately I had a small 12V fan in stock, so I could easily attach that to the sower supply. The fan I'm using is 40 * 40 * 10 mm and is very quiet. So I went ahead and installed the fan on the now somewhat molested original case. Some hot glue and masking tape made that an easy job. Not a looker, but enough for testing.
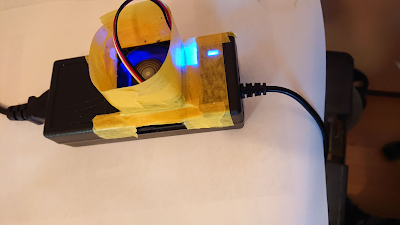 |
The somewhat molested power supply held together with hot glue and masking tape. |
As the original case was now in a very poor condition I went ahead and designed a new case in OpenScad. The dimensions of the new case is only slightly larger than the original one, though a little taller. I placed the fan close to the overheating diode, and the air outlet as close to the coldest part of the power supply. That way, with some luck, all warm components would get some airflow.
Printing the case took a couple of hours. The power supply barely got hand warm now. So the little fan did its work. Quite a good result for such a small fan - and very sketchy set-up.
 |
OpenScad model of the new power supply case. |
 |
Another OpenScad view of the case. |
 |
The new case is just a little larger than the old one. |
The finished case looks good and works great. I had a few issues with the tolerances, but fixed that with a little bit of sanding. I regret I didn't install a power switch on the case, as I don't want the fan to run 24/7. Luckily I can print an upgrade in an hours time. So when I get a switch ordered I will fix that.
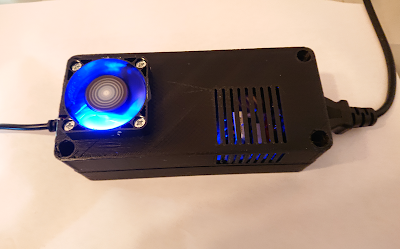 |
The finished upgraded power supply. |